Triggering a Change: Addressing the Multi-Material Challenges of Spray Triggers
Almost everyone has used a trigger sprayer with household cleaning products such as disinfectants, floor and surface cleaners at some point in their lives. You might not give them much thought, but they are a true marvel of engineering that creates efficiency and ease for our everyday cleaning tasks. Imagine how much more difficult it would be to control the amount of the product that is dispensed or to focus on a specific spot if you were only able to pour from the bottle, especially if it were a vertical surface such as a mirror or bathroom wall. Imagine the waste.
Spray triggers also play an important role in reducing the creation of new plastic and keeping plastic already made in use. For example, SC Johnson trigger bottles are designed to deliver more than 10,000 sprays, so they can be refilled and reused dozens of times.
But what happens when that trigger finally stops working? Unfortunately, because many are made with multiple materials to increase their durability and functionality, they can be a difficult if not impossible to recycle.
Why spray triggers can be hard to recycle.
Spray triggers have been around for many years. Early versions were quite fragile and reliant on brittle plastics, so much so the Philip W. Drackett Company, the original makers of Windex, originally sold the sprayers separately. As plastics improved and the cost of sprayers dropped, manufacturers were able to ship products with the sprayer already in the bottle.
In the late 1960s, spray bottles with trigger-style actuators appeared and quickly became popular, as this design was less fatiguing to use. When the trigger is pressed, the moving piston compresses the metal spring, so when you release the trigger, the piston is pushed back out of the gasket. These two strokes of the piston move the cylinder out again and contribute to the full pump cycle. This motion shrinks the cylinder and forces the fluid out.
Trigger-style actuators often include ten or more components, like valves, springs, gaskets, tubes, nozzles and more. Traditionally, many of these components can be made from a mix of different types of plastic and may have glass or steel components depending on the product’s needs. This is called multi-material, or multilayered product or packaging - and is where the recycling issue begins.
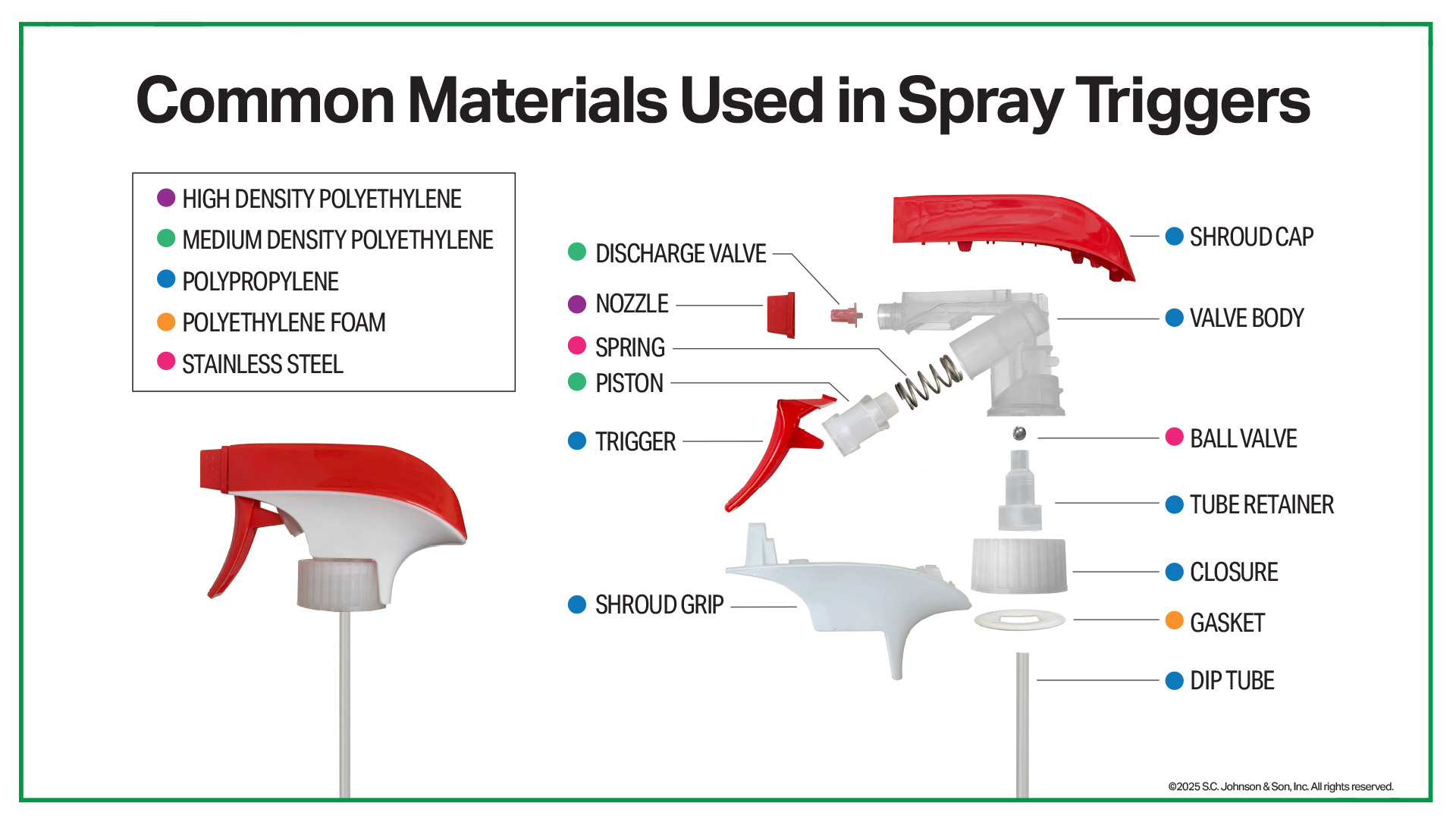
Why is multi-material product and packaging a recycling nightmare?
Multi-material products and packaging has grown in popularity across multiple industries, with up to 20% of plastic packaging consisting of multilayer materials. For instance, a typical food pouch might have layers of plastic for sealing, aluminum for barrier protection and paper for labeling. Small consumer items such as pens or scissors often come in blister packs, which are a mix of cardboard and clear plastic. Another example is the push-through, foil-and-plastic variant of blister packs often used for physician samples and over-the-counter pills.
The difficulty arises during the recycling process. Most recycling facilities cannot handle multilayer plastic, as the machinery and sorting processes used are not equipped to separate the different layers of tightly bonded materials efficiently. Manually separating them is labor-intensive and costly, making it impractical for large-scale operations.
Additionally, the presence of multiple materials in a single product can interfere with the recycling of other materials. Plastic coatings on paper products can clog recycling equipment and aluminum layers can complicate the melting process in glass recycling. Annually in the U.S. approximately 2.6 million tons of multilayer packaging end up incinerated or sent to landfills.
To address product end of life issues, companies are working to redesign products and packaging to be fully recyclable even when they are made to be reusable and refillable products. It’s a process called Design for Recycling.
How Design for Recycling helps.
Design for Recycling targets the same features as Design for Disassembly. In essence, the product or packaging is designed from the viewpoint of making it easier to sort, process and reuse the materials, rather than just hoping what is made works within the recycling systems after the fact. The aim is to create products and packaging that are easy to recycle, made from recyclable materials, and that can be transformed into new products through different manufacturing processes.
The good news is that companies are innovating to create dispensers made completely of recyclable materials. For spray triggers, that includes not only looking at the materials used, but also the size.
- Materials used: Traditionally, pumps in consumer goods contain an internal metal spring encased within the plastic, which makes them hard to recycle because recycling facilities need to separate the materials before processing them.
- Materials used: Different types of plastic
- Size: Getting to mono materials is important, because when you have so many small parts, the recycling infrastructure struggles to catch them.It’s better if it is just one whole part that can be recycled.
What does Design for Recycling look like in practice?
- SC Johnson EMF goal to design all our plastic packaging to be reusable, recyclable or compostable.[1]
- For example, SC Johnson has begun sourcing all-plastic triggers for several of its cleaning products in Europe, and as of 2023, 65% of SC Johnson’s packaging globally has been designed for recycling.
- As SCJ moves forward and with hopes to expand this change, all plastic, fully recyclable triggers will be the only triggers. Allowing for our liquid product’s containers to be 100% recyclable for the first time and resulting in less plastic waste overall.
While trigger sprayers were initially designed to make cleaning easier and reduce waste, their impact goes beyond convenience. The challenge has always been making such a small, complex component easier to recycle. However, because of design for recycling, progress is being made. This means more sustainable options are on the way—helping us waste less and recycle more.
[1] The current target is 100% but this target has been reassessed by both EMF and CGF to be very practically hard to hit. SCJ will likely change our target to 90% when we recommit.